In the intricate ecosystem of manufacturing facilities, maintaining optimal air quality and circulation is paramount. Beyond the obvious considerations of comfort for workers, proper ventilation plays a pivotal role in ensuring product quality, equipment longevity, and overall efficiency. While exhaust fans are commonly acknowledged for their role in expelling contaminated air, the importance of intake fans, particularly in creating fast and efficient air turns, is often overlooked. In this blog post, we delve into the significance of both exhaust and intake fans and how their synergy optimizes manufacturing environments.
The Crucial Role of Exhaust Fans
Exhaust fans are the unsung heroes of manufacturing environments. Their primary function is to expel stale air, fumes, dust, and other contaminants from indoor spaces, thereby maintaining air quality and creating a safer working environment. By continuously removing airborne pollutants, exhaust fans help prevent respiratory issues among workers and mitigate the risk of equipment corrosion and damage.
In addition to promoting health and safety, exhaust fans contribute to regulatory compliance by ensuring that manufacturing facilities meet ventilation standards set by relevant authorities. Failure to adhere to these regulations can result in fines, legal liabilities, and reputational damage for businesses.
Unveiling the Importance of Intake Fans
While exhaust fans are indispensable, their efficiency hinges on a complementary component: intake fans. Intake fans work in tandem with exhaust fans to facilitate the circulation of fresh, clean air throughout the facility. One of their critical roles is to create rapid air turns, which are essential for maintaining consistent air pressure levels within the manufacturing space.
Fast and efficient air turns, achieved through strategically positioned intake fans, prevent the formation of stagnant air pockets and ensure uniform distribution of temperature and humidity. This not only enhances the comfort of personnel but also optimizes the performance of sensitive machinery and processes that may be adversely affected by fluctuations in environmental conditions.
Moreover, intake fans play a pivotal role in energy conservation. By strategically drawing in outside air, they reduce the reliance on mechanical cooling systems, thereby lowering energy consumption and operational costs. This dual approach of exhaust and intake fans aligns with sustainability initiatives and fosters a greener manufacturing footprint.
Achieving Synergy for Optimal Efficiency
To harness the full potential of exhaust and intake fans, manufacturing facilities must adopt a holistic approach to ventilation system design and maintenance. This entails:
1. Strategic Placement: Positioning exhaust and intake fans strategically to create efficient airflow patterns and minimize energy wastage.
2. Regular Maintenance: Conducting routine inspections, cleaning, and servicing of fans to ensure optimal performance and longevity.
3. Investment in Technology: Embracing advancements in fan technology, such as energy-efficient motors and automated controls, to enhance overall system efficiency.
4. Compliance Monitoring: Staying abreast of evolving ventilation regulations and standards to maintain compliance and uphold workplace safety.
By integrating these practices into their operations, manufacturing facilities can create environments that prioritize worker well-being, product quality, and operational efficiency.
Conclusion
In the dynamic landscape of manufacturing, the significance of exhaust and intake fans cannot be overstated. While exhaust fans serve as the backbone of ventilation systems by expelling contaminants, intake fans play a pivotal role in creating rapid air turns and maintaining optimal air quality. By synergizing the functions of both types of fans, manufacturing facilities can foster environments that are conducive to productivity, innovation, and sustainability. As industries continue to evolve, embracing cutting-edge ventilation technologies will be instrumental in shaping the factories of the future, where efficiency and environmental stewardship go hand in hand.
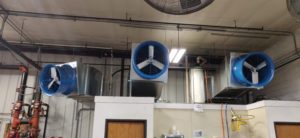
Three fans were required to provide the volume needed to cool this room